宝钛集团有限公司-智能制造促进企业快速发展
宝钛集团有限公司建于1965年,是国家“三五”期间为满足国防和尖端科技发展需要,兴建的重点三线企业。经过50年的发展,宝钛集团现已成为国内最大的以钛及钛合金为主的专业化稀有金属生产科研基地,形成了钛材、锆材、装备设计制造、特种金属等四大产业板块,形成了完备的以稀有金属加工为主体的产业群和产业链。
宝钛作为中国钛工业的龙头企业,多年来一直非常重视两化融合工作。2011年被陕西省工信厅评为“陕西省两化融合示范企业”,2014年被工信部遴选为“两化融合管理体系贯标试点单位”。宝钛制定了:“以创技术先进、管理一流、品牌国际化的世界一流钛业强企为宗旨,通过提升技术创新能力、集团管控能力,精益生产能力,使宝钛成为行业特色鲜明、国内一流、国际有影响力的有色金属材料研发、生产、服务综合提供商。”的两化融合总目标。
在提升精益生产能力方面,提出:“发展智能制造,提高生产过程管控水平,打造精益制造能力平台。建设完成生产设备数字化向智能化转变,同时实现PLC系统和智能仪表数据的实时采集,并通过MES系统实现生产过程的集中管控,提高集团的柔性生产制造水平。至十三五末,智能化生产设备占生产设备80%以上,产品生产数据准确率达97%以上,宝钛全线产品不合格品率控制在1%以下,生产周期平均缩短30%,在制品流动资金占用降低30%。”的两化融合分目标。
宝钛智能制造(数字化/智能化工厂)五级结构规划如图1所示:
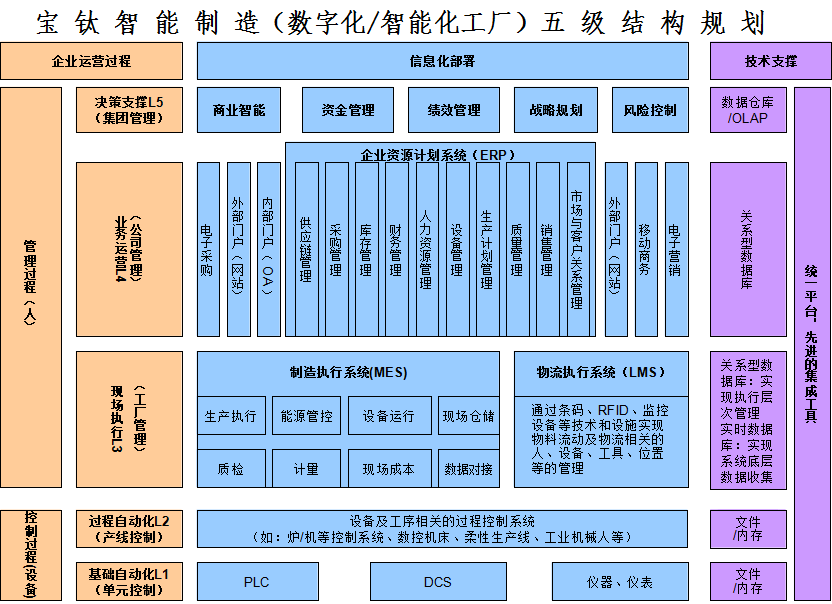
在深潜方面,尽管我国自行设计、集成创新、拥有自主知识产权的第一台深海载人潜水器——“蛟龙号”成功下潜到7000米深度,但因为国内制造水平较为落后,其关键子系统均为进口,如钛合金球壳引进自俄罗斯,机械手、灯光等设备引进自美国,成像设备引进自日本。其中最关键部分——供人活动的耐压球壳,在下潜到7000米深度时,要承受每平方米7000吨的压力,它使用了钛合金材料并在俄罗斯完成球壳的制造。我国正在组织力量攻克这一工艺技术,宝钛承担的“4500米潜水器载人球壳”的研制加工,已成功交付使用。
钛及钛合金在舰船上的应用可减少其维修成本和寿命周期成本,减轻船体的重量、增加有效载荷、提高舰船的可靠性和战术性。钛及钛合金在舰船上已应用的部位有耐压壳体、螺旋桨和浆轴、通海管路、阀及附件、各类管接头、热交换器、 装置、声学装置零部件、冷却器、冷凝器、发动机零部件、海水淡化装置、升降装置及发射装置等。宝钛研发的舰船及海洋工程用钛主要有:TA5-A、TA7、Ti-31、Ti-75、Ti-80、TC4、BT14、Ti-B19、Ti-60等钛合金的厚板、棒、管、环、饼、异形筒体件、铸件等。Ti-80、TA7、Ti-31钛合金系列厚板、棒材、锻件、厚壁管材和铸件,已形成批量生产。
要将钛及钛合金广泛应用到海洋工程装备和舰船领域,其加工制造过程非常重要。由于海洋工程装备和舰船的制造,具有大型化、制造精度高、质量可靠性要求高、管理过程复杂等特点,特别需要通过提高关键工序设备数控化率,使用先进的关键工艺装备,集成应用各种信息技术,达到对高技术海洋工程及舰船用装备的科研、生产、经营、管理、决策的全过程优化,形成具有自主知识产权的成套装备。
宝钛正在以智能化为突破口,以现有精密加工、高能焊接工艺为基础,采用人机智能交互、工业机器人等先进制造技术,在球型制造工艺和典型换热器制造工艺上做出突破,提升产品质量和生产效率。同时,集成智能CPS、智能MES、智能ERP、智能CAD/CAE/CAM/CAPP、智能仿真系统、物联网、传感器等先进技术,建设智能工厂,加快传统制造向智能制造的转型升级。
2. 钛、锆材板块,流程制造式生产“智能工厂”
在钛及钛合金、锆及锆合金材料的流程化生产方面,宝钛正通过制造执行系统(MES)、车间物联网现场控制系统 (SFCS)、 网络信息化系统 (IS)、企业资源管理系统 (ERP)、智能机器人系统 (Intelligent Robot)、 大数据系统(Big Data)等 “智能工厂”项目的建设以及系统集成整合,消除 “信息孤岛”,从而大大提高了宝钛生产过程的自动化和智能化水平,有效改善企业投资回报率,提高订单及时交货率、加快库存周转率,促进企业产品质量的提高和持续改进,以便最大限度的提高客户满意度,提升企业品牌形象和核心竞争力。确保国产大飞机用钛及钛合金材料的生产以及核动力锆及锆合金材料的生产。
已经在建项目有:各种设备包括(工控机、PDA、云终端、PC、移动终端等)实现人机交互跨终端访问;通过组件模块化的方式封装相关核心数据流结构、业务功能逻辑,实现流程化生产功能组件模块化;设置执行循环周期、执行结果报告发送信息、结果通知方式以及执行判断条件,自动排程生产任务;使用实时数据库平台、分布式数据库架构,满足实时访问全厂生产数据、高效压缩数据、长期存储历史数据、在线计算和统计、随时随地掌握生产状态的需求。
3. 工业控制系统信息安全保障
随着计算机和网络技术的发展,特别是信息化与工业化深度融合以及物联网的快速发展,使得工业控制系统信息安全问题日益突出。如果不重视和解决工业控制系统信息安全问题,将对工业生产运行、国家经济和人民生命财产安全造成重大隐患。甚至成为制约两化深度融合、中国制造2025等国家战略进程的因素。所以,工业控制系统的信息安全工作刻不容缓。
宝钛正通过实施工业控制系统信息安全保障项目,确保企业工业控制系统的可靠、稳定和高效运行。消除和降低由工业控制系统信息安全隐患可能导致的停产、减产和影响产品质量等情况所造成的经济损失,预防和避免设备及人身安全事故,促进生产本质安全。
采用 “固”、“隔”、“监”安全防护技术路线。固:从控制原理出发,保护控制变量、调节变量及过程数据安全,稳固控制系统根本运行安全;隔:通过对控制系统的安全及实际需求分析,建立安全分区,采用恰当的设备,将各层执行网络隔离,对多种工控以太网进行协议识别、控制及过滤,保证工控环境的生产控制安全;监:对于控制网内部针对控制网络通讯、操作行为、运行状态采用“白名单”的技术手段监控,并集中展示。实现:
3.1边界防护,保护关键设备系统
通过在L1基础自动化层与L2过程自动化层、L2过程自动化层与L3现场执行层之间部署工业防火墙,采用白名单技术,识别、控制及过滤非生产数据与流量,阻断非法访问,隔离木马、蠕虫病毒等恶意代码的进入,保护关键设备。
3.2网内监控,提升综合防护能力
在控制网内部部署工控信息安全监控系统,通过控制网内交换机镜像端口连接至一台监控引擎,在由引擎通过交换机连接到监控中心。引擎负责数据采集、分析、上传报警信息,监控中心管理引擎、接收报警信息和展示。
3.3隐患扫描,设备安全风险最小化
通过部署工控漏洞扫描系统,对宝钛股份工控系统/设备软件全方位测试和诊断,分析已知漏洞,挖掘未知漏洞,生成告警和系统分析报告,并通过隔离、监控、补丁等技术手段,使得工控系统内设备和软件漏洞风险最小化。
3.4集中管理,设备资产可视化管理
部署工业集中管理平台,通过网络与工业防火墙、工业监控引擎、工业交换机以及其他工控设备实现集中管理和监控。实现工控网络环境下的资产、通信和协议的可视化。
4. 其它方面的智能制造
4.1宝钛动力公司的能源数据采集及管理系统建设
宝钛作为高耗能企业,当前的能源管控措施少,效率低。所以,正在进行电力系统的能源管理项目,逐步实现所有能源管控。通过实施电力系统的能源管理项目,能有效实现电力负荷合理分配,保障企业生产经营。同时,提高能源循环利用率、减少外购、节能增效,减排减污、保护环境。
4.2计量控制中心的计量管理信息化系统建设
计量检测是设备运行、工艺、质量控制的重要环节,需进一步加强计量器具的管控手段。国内外宇航认证、国内军工认证均要求加强计量检测设备的动态、有效管理。所以,迫切需要建立健全及时、有效、完整、统一的测量设备管理系统,为企业的正常生产保驾护航。通过建立完善的测量设备信息数据库,及时掌握测量设备的工作状况和相关数据,实现计量管理信息的共享,方便查询和使用,提高计量器具的自动化管理水平,确保生产工艺准确性。
4.3档案室的档案电子化数字化管理系统建设
目前,宝钛档案室文件43698卷,仍采用手工翻账方式,效率低下。国内外宇航认证、国内军工认证均要求快速调出原始档案,所以,迫切需要通过电子化、数字化、网络化等管理手段提高档案管理效能,实现快速查询、调阅相关档案。
4.4研究院的科研管理系统及资源库系统建设
宝钛研究院非常注重科研项目的实施过程控制,通过科研管理系统的建设,能够完成科研工作计划、任务分解、研发工作网上协作、项目进程监控、物料成本监控等科研业务,提高科研管理效率。同时,为了更好地跟踪国内外钛行业科研、标准体系、以及企业内部各种资源、信息的共享,宝钛研究院建设了中国知网资源库系统,方便科研人员查找最新的文献资料,为科研和工艺改进提供了良好的工作环境。
4.5研究院的计算机模拟软件应用平台建设
计算机模拟技术在材料加工行业已经得到广泛的应用,该软件技术能够对钛合金材料熔炼、锻造、挤压、轧制等冶金及塑性加工过程进行数值模拟。计算机模拟软件在企业范围内获得应用,可缩短试验周期,提高效率,节约资金投入,实现数据共享,由其是对新型钛合金材料的开发有指导和借鉴作用。宝钛研究院在已有的simufact软件基础条件上,充分利用计算机模拟软件功能,搭建起更大范围的应用平台,覆盖主要分厂技术部门,方便生产单位的材料加工模拟工作,提高工作效率、减少服务资源浪费,系统得到广泛应用。
总体来说,宝钛集团从两化融合角度总体规划,通过在企业生产、经营和管理的各个方面,应用智能制造技术,建设智能制造系统,提升设备自动化水平、生产产线过程控制水平和生产制造智能化水平,贯通企业上层管理和底层生产制造;促进企业的技术创新、管理与商业模式的创新,顺应“两化融合”发展的大趋势,充分利用信息化的渗透、融合和变革作用,优化产业结构,建立企业发展新模式,促进企业快速发展。