陕西法士特齿轮有限责任公司-节能重卡变速器离散型智能制造试点示范项目总结
发布于:2019-05-14 11:37:02 来源: 陕西高研院
1. 项目实施背景与状况
节能重卡变速器离散型智能制造项目是陕西法士特齿轮有限责任公司(以下简称“法士特”)实现“十三五”、“5221”战略目标的重要支撑(传统机械变速器收入占比50%、智能化与新能源产品收入占比20%、国际市场收入占比20%、资本市场和新业态收入占比10%)。通过项目实施自动化、数字化升级、智能化,实现节能重卡变速器研发、制造、物流、销售、服务全流程的系统化集成和智能化,达到缩减新品开发周期,降低研发和制造成本,提高全价值链的协同运营效率和产品质量保证能力,满足多品种小批量柔性生产的需求等目标。从而实现将自主知识产权的先进变速器及传动系统的设计、加工、装配等核心技术转化为企业核心竞争力,助推企业战略目标达成。
项目围绕节能重卡变速器产业化发展不断变化的需求,重点围绕四个核心能力的提升:
1) 建立基于仿真的协同研发平台,缩短研发周期;
2) 建立基于物联网的智能化、数字化生产车间,提升生产效率;
3) 建立基于信息化的精益生产模式,提高资源控制能力;
4) 建立基于网络化的远程运维服务模式,提升用户、产品状态实时反馈能力,形成闭环的企业价值链。
2. 项目主要实施内容
2.1三维仿真建模技术的示范应用
针对产品系列化发展需求,项目设计采用三维仿真建模技术,从整体上对装配线体平面及空间布局进行三维模拟仿真,以构建模块化、标准化设备单位为目标的智能装配车间,并针对装配中关键工序点,进行动态仿真,真实模拟,再结合多学科设计优化方案对装配线体进行综合优化,从而得到切实可行的最优化方案,为后期方案的顺利实施提供了保障,极大地压缩了设计周期及成本。该技术在法士特公司中间轴弹性销及四方键自动上料压装、中间轴前后轴承自动在线压装及上盖总装与后盖总装机器人柔性自动拧紧单元均有应用,如图1所示,并将进一步应用在其它生产单元的改进设计。
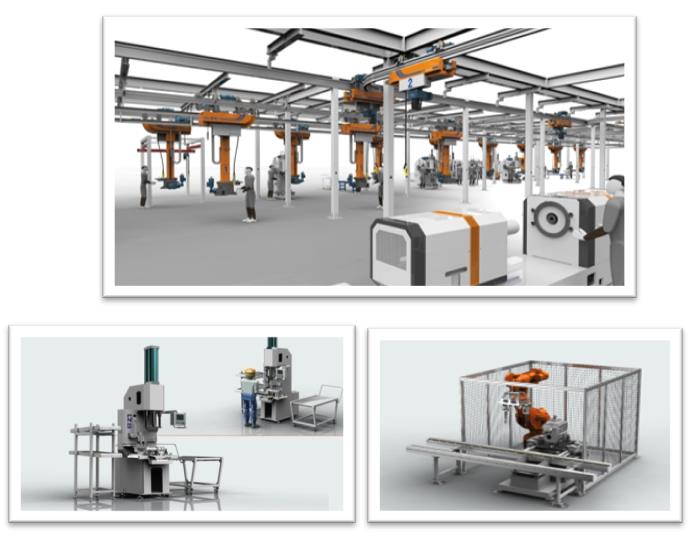
图1项目三维设计仿真
2.2智能装配技术的示范应用
法士特与中科院沈阳自动化研究所联合研制建设的一条设备自动化、控制智能化、管理信息化的变速器装配线顺利投入使用,极大地提高了变速器的产品装配效率和质量。装配线首次采用智能化J-HOOK悬挂式机械臂系统,智能机械臂采用三轴联动高精度控制,可满足装配中多种装配姿态需要,且物流通畅,实现了全程自动作业。装配控制系统通过DECA总线和PROFIBUS DP总线进行上位机控制及与输送小车的数据通讯,每台J-HOOK机械手均使用独立可编程控制器及相应的扩展模块,实现对其运行的精准控制与信号采集;该系统轨道全程铺设编码尺,每台小车装有射频读写头,读写头通过对绝对位置条码的扫描,保证小车的精确走位,如图2所示。该项技术自主研发,填补了国内技术空白,在变速箱行业内实属首次应用,系统自动化水平已达到国内领先、国际先进水平。
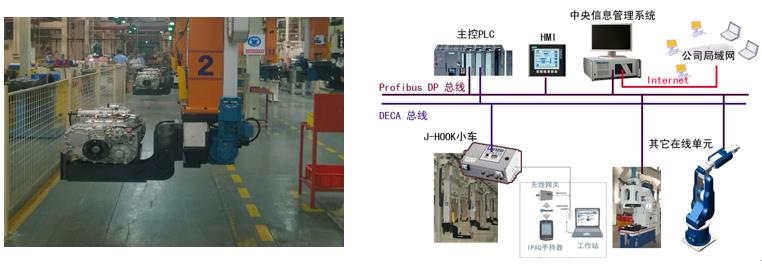
图2 项目智能装配系统
2.3机器人与其他多学科技术的高度集成示范应用
机器人在零件机加工的应用方面。项目已对11条生产线进行了自动化、智能化改造,并广泛采用了在线检测及SPC技术对齿轮跨棒距、跳动、壳体孔径及位置度等关键尺寸的测量、、数据采集及统计分析,同时还采用了零件自动输送及装夹技术,并对已有机床进行硬件及电气改造以满足与机器人的集成要求;机器人与数控机床集成主要采用了cc-link集成系统(通讯协议)、I/O总线系统,通过通信交互系统可以实现机床与机器人的信号互通,以及准确的传达各种指令。
机器人在装配过程的应用方面。装配线首次配备多台六自由度机器人,将机器人技术与其他多学科技术相结合,实现了多方面的应用突破。其中,机器人与拧紧机集成应用形成柔性智能拧紧单元,实现了多品种智能柔性拧紧,快速换产0秒切换,极大提高了装配效率及拧紧精度,是重卡变速器领域的首次应用;项目实现了机器人多工位的转线搬运和精准装配集成功能,各自动装配单元的机器人动作均可实现与J-HOOK机械手总线的实时通讯,通过智能传感与控制定位, J-HOOK机械手负责变速器壳体的精确定位,机器人负责轨迹控制,直至将工件完全放入指定位置,提高了装配的准确性,使无人化工位占有率达30%以上,极大节约了人力资源,项目机器人的集成应用如图3所示。
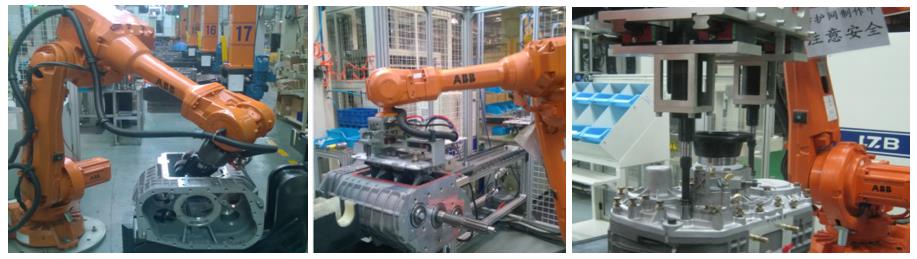
图3 项目机器人的集成应用
2.4智能检测技术的示范应用
通过采用最前沿的技术,对标国际汽车零部件企业的标准,零件机加工过程实施了在线快速检测SPC项目,实现公司壳体、齿轮等零部件在线快速检测、存储、公司内联网共享、实时分析等功能。通过对产品质量过程进行检测和调整,使全过程处于受控状态,以保证质量。总成下线也采用智能化测试台,具有测试程序配方功能、变速器速比检测功能、功能开关检测及报警功能、里程表传感器检测功能、条码扫描自动选择型号功能、试验台测试数据报表功能、远程控制功能等。通过信息系统的调度,试车输送线自动完成与试验台的信息交互及工件交换,加载下线试验台首次采用强制试车功能,促进和保障产品质量的提升。
2.5智能物流与仓储装备的示范应用
为节约厂房资源,物流输送采用空中立体配送的模式,零件可通过空中输送线自动抵达各装配工位,全线实现单台配送,从根源上规避了错配漏配的风险,并且大幅节约了人力和空间资源;同时,物料配送采用WMS与SPS相结合的精益拉动系统,使自动化仓库作业效率得到最大发挥,降低库存量,提高物料周转率,推进精益化生产水平。
2.6装配车间数字化升级示范应用
基于数字化车间建设需求,已在装配车间搭建智能化网络管理平台,实现了数控设备、数据存储系统和生产制造业务流程的系统管理;基于智能化、信息化技术,实现整个生产制造和物流管理过程可视化,使公司内各部门、各环节更加紧密协同;生产任务编排更加科学合理,保障新产品能够高质量、高效率、低成本交付。公司参与的“支持批量定制生产数字化车间动态管控平台及装备研发与应用技术项目”荣获国家科学技术进步二等奖,同时借鉴装配过程数字化经验,项目将进一步拓展机加工车间的数字化改造。
2.7信息系统规划和实施示范应用
法士特公司2016年主题为两化推进年,公司聘请了知名信息化研究院给公司制定了信息化规划,为本项目的实施提供了智力保障。以先进制造方式为主线,以打造价值链整体竞争力、提升企业职能业务能力为目标,通过强化基础管理、优化业务流程,深化信息技术应用和数据资源开发利用等全要素互动创新和持续改进。通过PLM、ERP、MES、WMS等系统平台的搭建及数据的互联互通,消除信息孤岛,实现核心模块的数据共享和准确传递,打通企业生产全过程信息通道,实现数据集成、业务协同,并以此为基础,促进CPS物理信息系统形成,推进业务管理能力和集团管控能力的持续提升。
3. 项目实施成效
3.1项目相关指标统计
1) 通过以上新技术的应用,项目产品一次装箱合格率由原来的96%提高至99.5%,售后PPM值同比下降30-40%;
2) 多工位采用智能无人装配,节约人力资源。该项目与同类项目比较,操作工由60人减少至40人 ,无人化工位占有率达到30%以上;
3) 首创空中物流模式,采用立体配送及空中机械手装配等精益化、集约化方案,占地面积减少50%;
项目当前实施成效的其他主要指标情况如表3-1所示。
表3-1 项目指标变化统计表
智能制造实施前后成效对比 | 成效评价项目 | 实施前 | 实施后 | 变化情况 |
运营成本 (万元产值可控成本) |
XXX元/万元 | XXX元/万元 | 降低9% | |
生产效率 (每日人均产出) |
XX台 | XX台 | 提高20% | |
产品研发周期 | XX个月 | XX个月 | 缩短25% | |
产品不良率 (PPM) |
XXXX | XXXX | 降低30% | |
能源利用率 (万元产值能耗) |
0.0XX吨标准煤 | 0.0XX吨标准煤 | 降低2% |
3.2项目社会及经济效益
项目通过智能化改造升级,在盘活存量能力的同时,产生了较大的社会效益与经济效益,主要体现在以下4个方面:
1) 项目采用科技前沿技术,设计秉承安全、环保的科学理念,使用的新技术、新材料、新工艺等均符合国家安全环保法律法规;项目首次采用中间轴卧式自动压装,解决了传统立式压装过程中潜在的安全风险,将工人操作安全隐患降为0,体现了以人为本的设计理念。
2) 自主研发智能全自动机械手、斜齿对齿等技术填补国内技术空白,智能装配线总装效率高,降低了工人劳动强度。
3) 由于制造装备的先进性,项目下线产品质量一致性好,产品故障率以及售后维修保养成本降低了30-40%,备受顾客青睐,进一步提升了企业的品牌价值,订单量不断加大;智能装配线的投入使用至今已累计为企业生产变速器总成36万台,累计实现产值54亿元。
4) 项目智能化水平与质量保证能力的提升,也使企业顺利通过世界一流主机厂家的质量审核(如戴姆勒、沃尔沃等),产品远销欧美市场,企业国际化竞争力进一步增强。
4. 实施经验
4.1引入了信息系统顶层设计方法
“顶层设计”源于自然科学或大型工程技术领域的一种设计理念,项目针对具体的设计对象,运用系统论的方式,注重规划设计与实际需求的紧密结合,强调设计对象定位上的准确、结构上的优化、功能上的协调、资源上的整合,确保设计目标的实现。
4.2采用先进的柔性化、集成化、智能化生产方式
该项目以智能化与精益生产思想相结合的生产方式取代了传统的大批量制造模式,广泛采用自动化、智能化手段,基于快速检测、夹具标准化、装配工艺数字化、工艺仿真、自动编程、生产线精益布局和精益物流等核心技术的集成应用,使得生产组织方式、设备运行更加适合多品种、小批量的柔性生产需求。
4.3实现研发、工艺、制造、物流、销售服务的信息化集成
制造企业信息化建设是一项庞大的系统工程,包含的信息及数据资源非常广泛,项目以应用集成为核心,符合面向服务架构(SOA)理念,以企业服务总线(ESB)、业务流程管理(BPM)、数据服务总线(DSB)为核心组件的应用集成平台,从数据层面、应用层面、流程层面进行全面的应用集成,整合企业信息的应用及服务,促进公司核心价值链的协同高效运作。