汽车智能制造技术应用及智能工厂案例
发布于:2018-09-26 17:08:00 来源: 陕西高研院
智能制造是贯彻落实《中国制造2025》的战略部署,是两化深度融合的主攻方向,是增强我国制造业发展优势的关键所在,大力发展智能制造是加快制造强国建设步伐,加速推动汽车产业由规模速度型向质量效益型转变的重要途径。
目前,我国汽车行业推进智能制造工作取得了积极进展和成效。工业和信息化部开展了智能制造试点示范专项行动,通过创新驱动强化智能制造 核心装备的自主供给能力,不断完善智能制造标准体系,逐步夯实工业软件等基础支撑能力,通过示范带动构建了集成服务能力,通过集成应用提升了新模式应用水平。实施专项行动3年来,累计支持了33项汽车行业智能制造试点示范项目,占支持项目的16%,涵盖了传统及新能源汽车乘用车、商用车、客车等以及智能网联汽车等领域,以及发动机、变速器、底盘系统、动力电池、汽车电子、轮毂、轮胎、汽车玻璃等关键零部件,项目成果显著,示范带动和集成应用辐射放大作用十分突出。
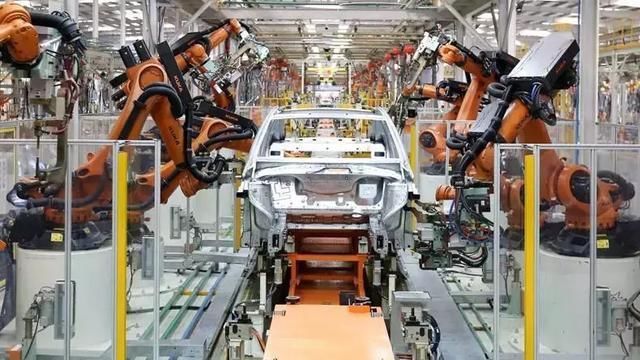
当前,以下智能制造技术在汽车整车及零部件制造领域均已开始普及应用:
1、智能制造技术逐渐进入整体工厂阶段
我国工业制造发展至今经历了“工业1.0-机械制造”、“工业2.0-流水线、批量生产,标准化”、“工业3.0-高度自动化,无人/少人化产”和“工业4.0-网络化生产,虚实融合”等阶段。从传统制造走向大规模个性化定制,由集中式控制向分散式增强型控制的基本模式的转变,要求建立一个高度灵活的个性化、数字化和高度一体化的产品与服务生产体系。汽车整车及零部件制造业要实现个性化产品的高效率、批量化生产,必需综合兼顾物料供应协同、工序协同、生产节拍协同、产品智能输送等诸多环节,围绕智能制造技术的一体化整厂设计是“智慧工厂”建设的必然选择,也是实现工业4.0的重要基础和保障。
2、智能自动化柔性生产技术
随着科学技术的发展,消费者以及社会对产品功能与质量的要求越来越高,产品更新换代的周期越来越短,产品的复杂程度也随之提高。为了提高制造业的柔性与效率,在保证产品质量的前提下,缩短产品生产周期、降低产品成本,智能自动化柔性生产线在行业内得到普及。智能自动化柔性生产系统由信息控制系统与制造装备单元组成,是能适应制造工件对象变换的自动化生产线。柔性生产线可以增强生产线的适应性,使生产线的布局更能适应消费需求的变化。
3、智能自动化系统控制软件技术和信息技术
智能自动化系统控制软件技术是实现智能化的 核心所在,它利用信息技术,通过现场设备总线、现场控制总线、工业以太网、现场无线通讯、数据识别处理设备以及其他数据传输设备,将智能自动化装备的各个子系统连接起来,使生产流程进一步由自动化提升到智能化,使智能自动化生产线从本质上实现安全生产、柔性制造。
4、协作机器人的普及化
随着智能自动化生产线系统行业的持续发展与优化升级,关键环节的的协作机器人应用将得到进一步的提高。业内数据统计表明,近几年协作机器人的应用取得了爆发式的增长。这些新推出的协作机器人具有轻巧、廉价的特点,结合了先进的视觉技术,将为生产工作提供更多感知功能。
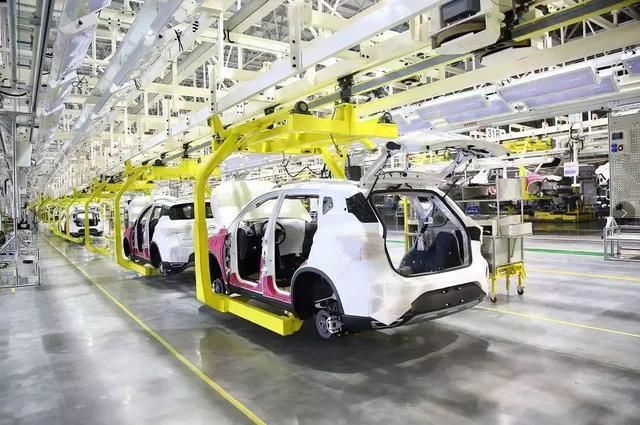
汽车智能工厂案例
众所周知,工业4.0的两个主题是智能工厂+智能生产。在工业4.0背景下,汽车工厂将实现网络化、分布式的生产设施,控制生产过程中不断出现的复杂性,人、机器与资源之间会有直接的交流。与此同时,高度标准化、模块化的设备及系统将大幅节省汽车生产制造中的成本,机器人可以从事高强度持续性的工作,依托于传感器、3D打印等技术 大大提高零部件生产加工及工序中的精密度,降低失误率及风险。
1、宝沃:中德智造示范工厂
作为“德国制造”的一个代表,宝沃汽车实现了工业4.0智能工厂的部署,以先进的智能制造体系,入选工信部发布的“2017年中德智能制造合作试点示范项目”。
宝沃智能工厂采用全球先进的八车型柔性化生产线,在具备强大灵活生产性能的同时可实现多车型共线生产,并打造个性定制化车型的生产及开发,集冲压、焊装、涂装、总装、检测和物流六大工艺流程于一身。
宝沃的柔性化生产拥有17种颜色系统,可实现汽油、混合动力、纯电动等左右舵车型生产并且,其“柔性制造”可实现自行优化整体网络,并自行适应实时环境变化及客户个性化需求。整个车间拥有先进的自动化技术,近550台机器人完成在冲压、传输、车身点焊、油漆喷涂等过程的作业。通过智能化生产体系,以及物联网化的生产设施,最终实现企业供应链,制造等环节数据化、智慧化,以及达到高效生产及满足个性化需求的目的。
在质量管控方面,宝沃智能工厂在德国DIN、VDA严苛的质量标准下,开发了BQMS宝沃质量管理系统:通过18道在线控制点,34道质量控制点,16个质量门,1075项整车检验,运用自动化、信息化技术和云平台,实现整车质量保证体系数字化,并在智能物流方面实现了大规模个性化定制生产、订单交付周期最短23天。
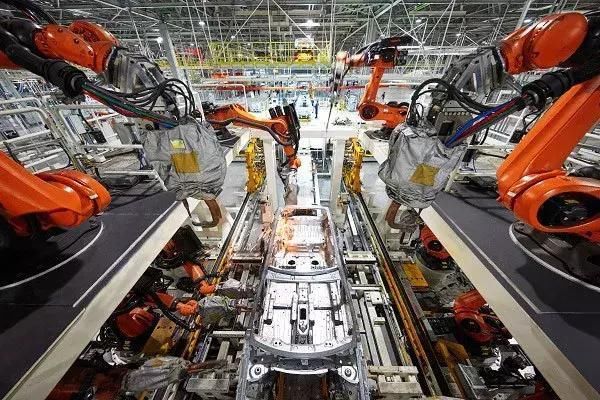
2、法士特:“智能生产系统”自主造
与其他企业外包或外购智能生产系统不同,法士特智能化生产车间完全由自己编程、制造而成。
据了解,法士特在生产线上引入模块化的理念,实现了控制器、气动门等部件的标准化运作和生产线的灵活运用。法士特最新投入使用的自动装配悬臂线,将工业自动控制、通讯、智能机器人、定扭紧固、信息控制、测试等多项技术结合应用,多工位实现自动化装配。与此同时,法士特还不断推进云端技术,将所有智能机器人和生产线数据进行网络监控和管理,实现后台操作、调整机器人工况数据,还可进行跨厂之间的信息对比。
首条智能生产线投入使用后,线上工作人员从17人减少到7人,从每天最多生产450套产品提升至现在的750套;不仅生产效率提高40%,产品一致性也得到进一步保证。此外,法士特自动装配悬臂线投入使用后,一次装箱合格率提高3%,装配线产能提高25%,占地面积节约27%,有效降低工人的劳动强度,大幅提升了产品装配自动化和智能化水平。
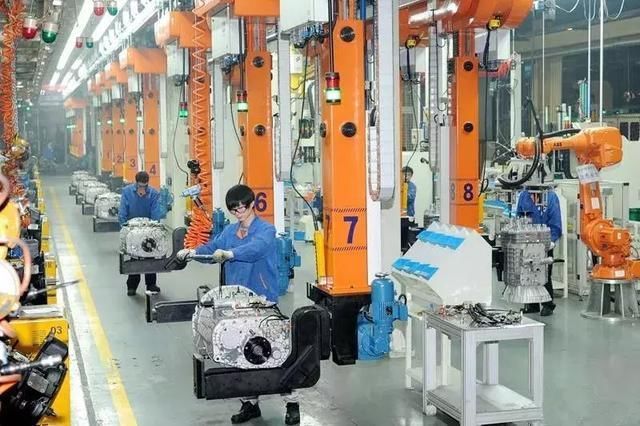
3、广汽传祺:安全清洁智慧的工厂
广汽传祺杭州工厂秉承“工业4.0”的智能制造理念,历时13个月建设,遵循“一次规划、分步实施”的原则,以广汽传祺世界级生产方式为 核心,糅合全球领先的研发技术、科学管理方法和严谨的质量控制体系,采用独创的VIDM(可视化、信息化、数字化、智能制造)系统,打造了一座安全、清洁、智慧的工厂。
其中,冲压车间采用全自动伺服高速生产线及直线7轴高速机器人,实现了深拉延、高品质、高柔性、低噪环保的完美结合;焊装车间首次采用CO2机器人自动弧焊工艺,配备全球领先的机器人及机器视觉AI技术,可实现高精度、多车型柔性共线生产;涂装车间采用世界领先的Ro-Dip 360度翻转前处理电泳线,壁挂式机器人喷涂系统采用紧凑型两道色漆绿色环保喷涂技术,充分体现传祺的“绿色工厂”理念;总装车间采用L型布局,自主设计底盘自动合装设备,实现玻璃自动涂胶、安装及座椅自动抓取安装等技术,构建了具备世界水平的广汽传祺标杆工厂。
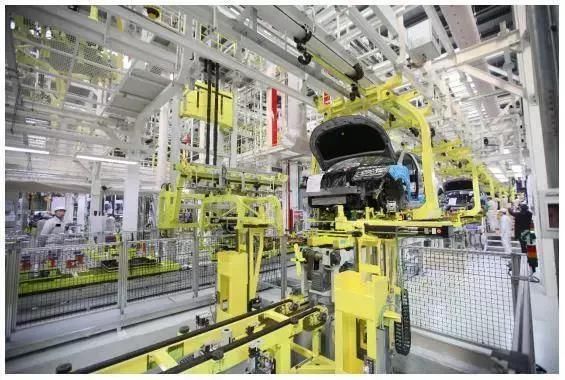
4、奥迪:颠覆传统的汽车工厂
奥迪一直将科技作为产品的卖点,这一次奥迪将科技发挥到了极致,为我们描绘出一座未来汽车工厂--奥迪智能工厂。在这座工厂中,我们熟悉的生产线消失不见,零件运输由自动驾驶小车甚至是无人机完成,3D打印技术也得到普及……这样一座颠覆传统的汽车工厂都有哪些黑科技?
零件物流是保障整个工厂高效生产的关键,在奥迪智能工厂中,零件物流运输全部由无人驾驶系统完成。转移物资的叉车也实现自动驾驶,实现真正的自动化工厂。在物料运输方面不仅有无人驾驶小车参与,无人机也将发挥重要作用。
在奥迪智能工厂中,小型化、轻型化的机器人将取代人工来实现琐碎零件的安装固定。柔性装配车将取代人工进行螺丝拧紧。在装配小车中布置有若干机械臂,这些机械臂可以按照既定程序进行位置识别、螺丝拧紧。装配辅助系统可以提示工人何处需要进行装配,并可对最终装配结果进行检测。在一些线束装配任务中还需要人工的参与,装配辅助系统可以提示工人哪些位置需要人工装配,并在显示屏上显示最终装配是否合格,防止出现残次品。
奥迪智能工厂发明的柔性抓取机器人不同于现阶段的抓取机器人,该机器人最大特点在于柔性触手,这种结构类似于变色龙舌头,抓取零件更加灵活。除了抓取普通零件外,柔性抓取机器人还可以抓取螺母、垫片之类的细微零件。
未来奥迪智能工厂将借助VR技术来实现虚拟装配,以发现研发阶段出现的问题。借助VR设备,设计人员可以对零件进行预装配,以观测未来实际装配效果。此外,数据眼镜可以对看到的零件进行分析,这套设备类似装配辅助系统,发现缺陷与问题。数据眼镜可以对员工或者工程师进行针对性支持。
在奥迪智能工厂,3D打印技术将得到普及,到时候汽车上的大部分零件都可以通过3D打印技术得到。目前用粉末塑料制造物体的3D打印机已经被制造出来,下一阶段发展的是3D金属打印机。 奥迪专门设计了金属打印试验室,对此技术进行研发。
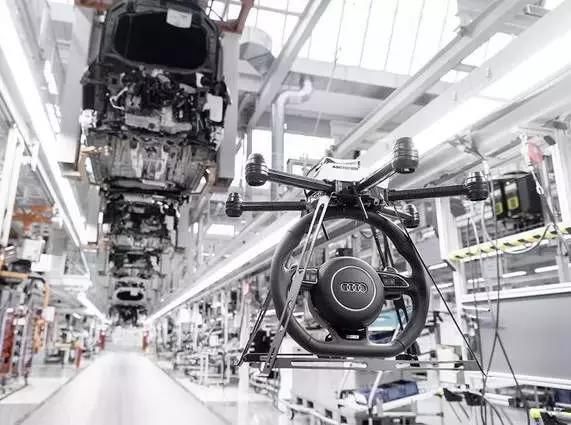